Porosity in Welding: Identifying Common Issues and Implementing Best Practices for Avoidance
Porosity in welding is a prevalent problem that usually goes unnoticed up until it creates significant problems with the stability of welds. In this discussion, we will explore the crucial aspects adding to porosity formation, examine its detrimental effects on weld efficiency, and talk about the ideal techniques that can be taken on to lessen porosity event in welding processes.
Usual Root Causes Of Porosity
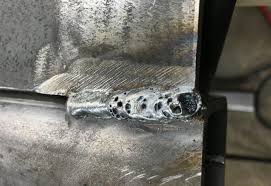
Another regular wrongdoer behind porosity is the presence of contaminants on the surface area of the base steel, such as oil, grease, or corrosion. When these pollutants are not successfully eliminated before welding, they can vaporize and become trapped in the weld, creating defects. Moreover, using unclean or damp filler products can present impurities into the weld, adding to porosity concerns. To reduce these common root causes of porosity, detailed cleaning of base steels, correct securing gas option, and adherence to optimum welding specifications are vital methods in attaining high-quality, porosity-free welds.
Impact of Porosity on Weld Quality

The presence of porosity in welding can significantly endanger the architectural integrity and mechanical buildings of welded joints. Porosity produces spaces within the weld steel, deteriorating its general strength and load-bearing capacity. These gaps function as stress and anxiety concentration points, making the weld a lot more susceptible to fracturing and failure under used lots. Additionally, porosity can minimize the weld's resistance to rust and various other ecological variables, even more decreasing its durability and performance.
One of the key consequences of porosity is a reduction in the weld's ductility and strength. Welds with high porosity levels often tend to display lower effect stamina and minimized capability to warp plastically before fracturing. This can be specifically concerning in applications where the bonded parts go through dynamic or cyclic loading conditions. In Recommended Reading addition, porosity can hamper the weld's capability to successfully send forces, causing premature weld failing and possible security risks in crucial frameworks.
Ideal Practices for Porosity Prevention
To enhance the architectural integrity and quality of welded joints, what certain measures can be executed to reduce the occurrence of porosity during the welding process? Porosity prevention in welding is vital to ensure the stability and stamina of the last weld. One reliable technique appertains cleansing of the base steel, eliminating any type of impurities such as rust, oil, paint, or wetness that can bring continue reading this about gas entrapment. Making certain that the welding equipment is in excellent problem, with tidy consumables and proper gas circulation rates, can also substantially decrease porosity. Additionally, preserving a stable arc and controlling the welding specifications, such as voltage, present, and travel rate, assists create a regular weld swimming pool that decreases the danger of gas entrapment. Utilizing the appropriate welding technique for the certain material being bonded, such as readjusting the welding angle and weapon setting, can further protect against porosity. Routine examination of welds and prompt remediation of any kind of problems determined during the welding process are necessary methods to avoid porosity and create top quality welds.
Significance of Appropriate Welding Methods
Executing correct welding techniques is extremely important in guaranteeing the architectural integrity and top quality of welded joints, constructing upon the foundation of reliable porosity avoidance measures. Excessive warmth can lead to enhanced porosity due to the entrapment of gases in the weld swimming pool. Furthermore, utilizing the proper welding specifications, such as voltage, present, and take a trip rate, is crucial for attaining audio welds with very little porosity.
Moreover, the option of welding process, whether it be MIG, TIG, or stick welding, should line up with the particular demands of the project to guarantee optimal outcomes. Appropriate cleansing and prep work of the base steel, along with choosing the best filler material, are additionally essential elements of skillful welding strategies. By adhering to these ideal methods, welders can minimize the danger of porosity formation and generate high-grade, structurally sound welds.
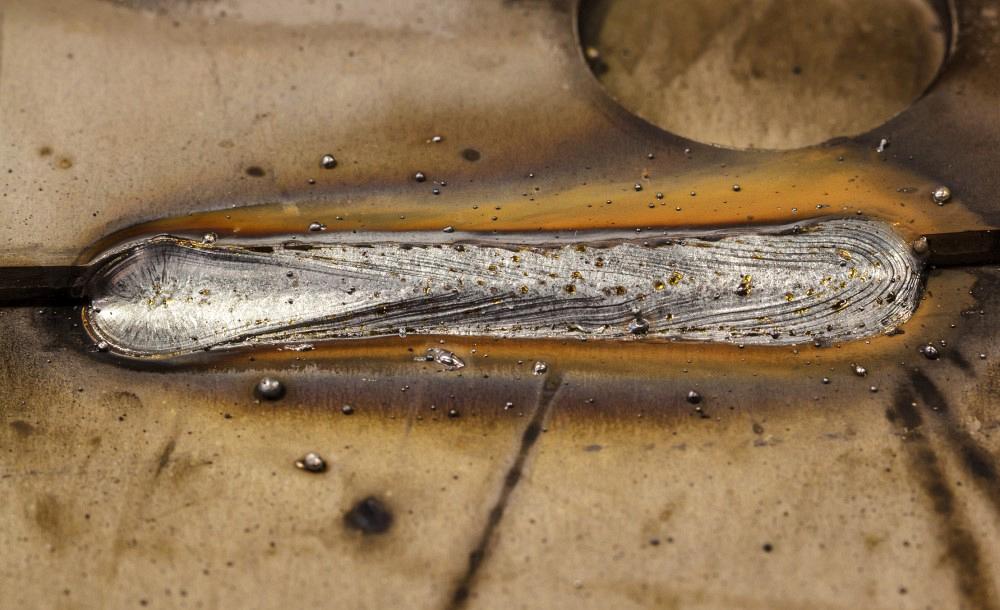
Checking and Top Quality Control Actions
Checking treatments are important to identify and prevent porosity in welding, making sure the toughness and sturdiness of the last item. Non-destructive testing techniques such as ultrasonic screening, radiographic screening, and aesthetic inspection are frequently utilized More Help to determine possible defects like porosity.
Conducting pre-weld and post-weld inspections is additionally vital in maintaining quality control criteria. Pre-weld assessments entail validating the materials, equipment settings, and tidiness of the workplace to stop contamination. Post-weld assessments, on the other hand, examine the last weld for any kind of issues, including porosity, and confirm that it meets defined requirements. Implementing a detailed quality assurance plan that consists of extensive testing procedures and examinations is vital to decreasing porosity concerns and making sure the overall high quality of bonded joints.
Verdict
In final thought, porosity in welding can be an usual problem that affects the high quality of welds. By identifying the common causes of porosity and implementing ideal methods for prevention, such as correct welding methods and testing actions, welders can make certain high top quality and trustworthy welds. It is vital to prioritize avoidance techniques to minimize the event of porosity and preserve the honesty of welded frameworks.